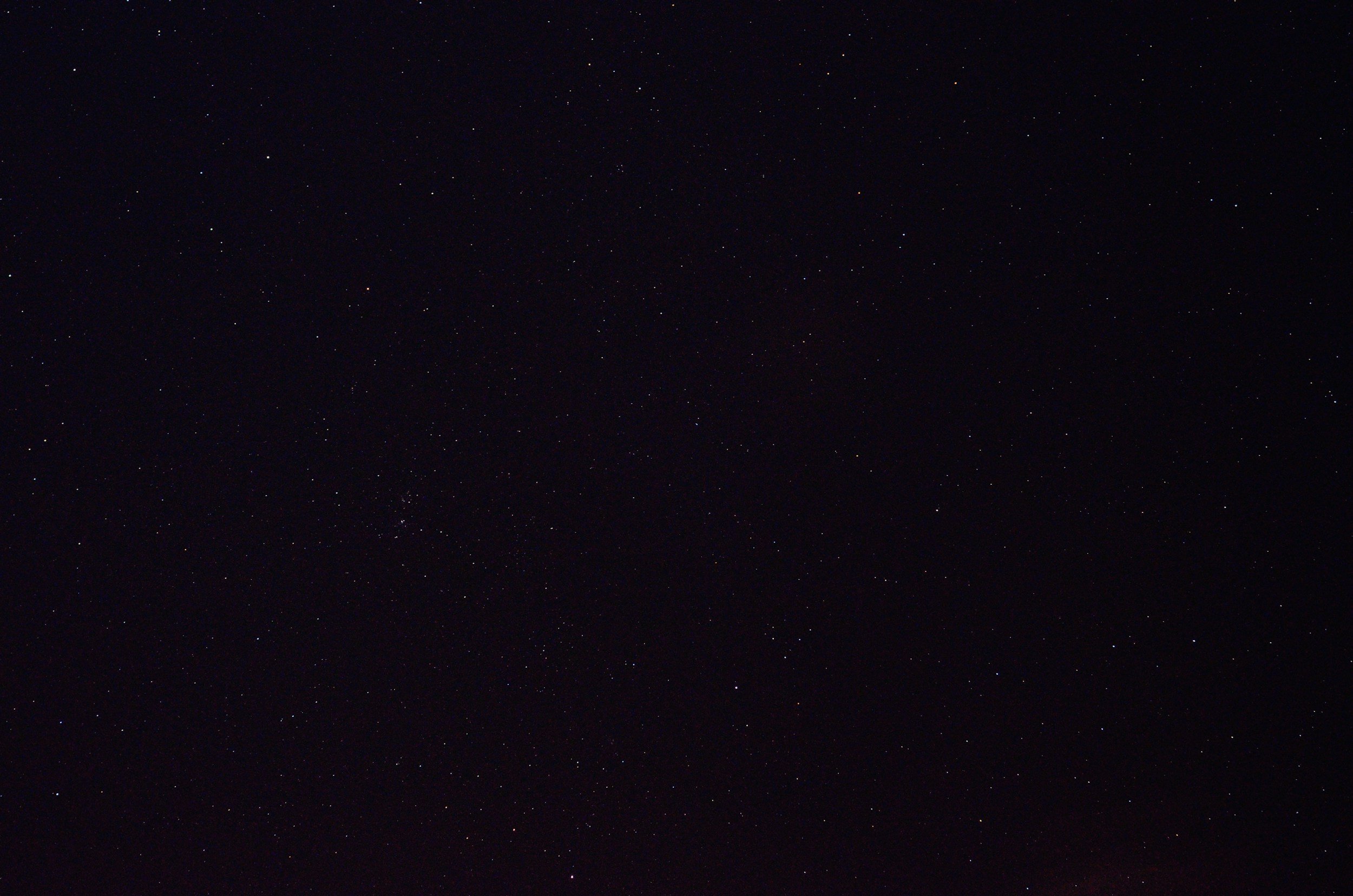
Vendor Guide
Premium Blank Vendor Guidelines
PREMIUM BLANK requires the Vendor to guarantee the products shipped to PREMIUM BLANK for one (I) year against craftsmanship and material. This guarantee is only for manufacturing defects. It does not cover normal “wear and tear. If a manufacturing defect occurs, Vendor is responsible for replacing the item or crediting PREMIUM BLANK. If an item is deemed “normal wear and tear” the Vendor is not responsible.
Although PREMIUM BLANK inspects all orders, the Vendor must still guaranty the product, even if shipment is only sampled. The guarantee is for all pieces produced.
Upon request, PREMIUM BLANK will provide Vendor with the following:
An itemized report with a description and quantities of each defective item;
An example of a defective product;
The return of all defective product for which PREMIUM BLANK is seeking on the warranty statement. Transportation costs to be paid by the Vendor.
Once PREMIUM BLANK has received Vendor’s credit memo or payment, all product covered under warranty will be destroyed or returned at the Vendor’s discretion.
I. COMPLIANCE
PREMIUM BLANK reserves the right to charge back any expense, loss or damages incurred if Vendor fails to follow the Vendor Policy.
Charge backs will be issued by PREMIUM BLANK pursuant to the attached Reject or Damages Report. PREMIUM BLANK reserves the right to issue reasonable Charge Backs included in Non-Compliance Reports. Standard Chargeback rates are:
Inspection Fee of $15 per hour.
Handling fee of $100 per defective shipment
II. PRODUCT DEFECTS
General Appearance
The overall general appearance must be acceptable
Facings must be deep enough to prevent rolling out
Stripes and plaids must match, unless otherwise specified
Fabrics with naps must be cut in the same direction
There are to be no substituted or missing parts, unless authorized
There are to be no components or construction used in sewn product that becomes prematurely defective or nonfunctional as a result of normal product use and care.
There are to be no shaded parts throughout
There is to be no off-standard colors used; all must fall within Acceptable shaded bands
Any deviation of a production product that compromises the intent of design, wear-ability or sale-ability of the product, will be categorized as a defective product.
Construction
There are to be no incorrect bar-tack positions or types from those specified
There are to be no raw or untrimmed edges, except by design
There are to be no twisted or non-aligned sleeves which appear twisted
There are to be no incorrect bar-tack positions or types from those specified
There are to be no incorrect construction methods used from that which is specified or which is inappropriately used for fabric or function
There are to be no parts sewn on unevenly, in the wrong direction or in the wrong location
There are to be no unsymmetrical cables, pattern and designs when not intended
All seams MUST be joined face to face, except where permitted by special circumstance (felled seams are excluded)
All snaps, rivets, eyelets and trims must be securely fastened
Matching
All patterns must match unless otherwise specified
There is to be no uneven stripe alignment
All plaid, horizontal stripes or logos must match as specified
Seams
All shell seams, unless otherwise specified must be face to face joined
All lining join seams are to be serged
All seams are to be constructed with 10-12 stitches per inch (SPI) unless otherwise specified
All edges must be finished (taped, overlock, stitched or otherwise finished) — there are to be no raw edges anywhere on the product, unless otherwise specified.
All threads must be trimmed and all tails pulled to the inside
All seams must lie flat and smooth
Rise seams must be face to face joined. All edges must be lock stitched and serged or 5-thread safety chain stitched
All top stitching must be matching, unless otherwise specified
All top stitching must be continuous, with no starting and stopping within the distance
All hem stitching must be even
All darts must be uniform in shape/length with no dimples at the end
All dart ends must be secure
Shoulder and back neck seams of knit garments must be stay taped
There are to be no crooked, puckered, curled, pleated, twisted, wavy or uneven seams (Certain fabrics or techniques will have tendency to do this and will be dealt with individually)
There must be no open seams
There are to be no excessively grinning” seams and no excessive puckering along seams
There are to be no uneven seam allowances or excessively bulky seams
No seams are to be stitched wrong side out, unless by design
Irregular Stitching
No concealed stitching is to show to the outside, unless otherwise specified
All contrast color stitching must be even and uniformly spaced
There are to be no broken stitches
Thread tension must not be excessively tight or loose
Double top stitching must be parallel and evenly spaced
There is to be no use of monofilament thread, unless approved
There are to be no skipped stitches on chain stitch
There should be no skipped stitches on lockstitch but a maximum of 1 per seam (2 if long seam) is allowable as long as it does not affect function
There are to be no needle cuts that appear objectionable or that could develop into a hole
There are to be no excessive and I or loose threads
No threads other than the specified color. size, type
No improper thread match, if match is intended
There is to be no inconsistent use of thread color within same product
Logos
Logos with a stitch groove must be properly aligned. Logos without stitch grooves must be skillfully executed
Logos must be the correct shape, size, color and position. The Logo must never be altered.
Stress Points
Stress points on the fly bottom must be bar-tacked to take strain from the zipper
There must be a bartack at the intersection of the seam and inseam of the shell, on the inside, within the seam allowance through all layers
Interface Lining
All stress points must be bar-tacked and / or reinforced, as necessary
Fusible interfacing must lie flat and not bubble
Interfacing must be used on collars, cuffs, plackets and waistbands, unless otherwise specified
Lining must not hang below the hem
Garment linings are to be swagged to the shell at underarm and crotch intersection
All edges of lining must be serged
Elastic
Elastic must extend to the fullest width without stitches breaking or binding on the body
Tunneled elastic must be stitched down or tacked to prevent twisting or rolling over
Pockets
Pocket bags must have sufficient depth for hands
All pockets must be evenly aligned
Pockets must be reinforced at upper corners
Drill holes must be sewn over or covered by seams
All free hanging pocket bags must be serged if the garment is lined and clean finished if the pocket bags are exposed
Pockets must not be noticeably uneven in size, shape or location
All pocket flaps must be properly shaped and set
The seam allowances of all pocket flaps are to be concealed under the topstitching and there are to be bartacks on each end of all flaps
There are to be no sewn in pleats or excessive puckers, except by design
Corresponding pockets must be horizontally even and aligned
All pocket closures must be correctly shaped and aligned
Zippers
Zippers must lay flat on product when stitched — There are to be no exposed or wavy zippers
Zipper parts must not be set improperly (backward, twisted, etc.)
Zippers must have stoppers
Buttons/Buttonholes
Buttons and buttonholes must be evenly spaced, unless otherwise specified
Buttons must be securely fastened
Buttonholes must be completely stitched around with clean and finished edges
Buttonholes must not be too small or too large for buttons
Buttonholes must be cut with a sharp knife
An extra button is to be attached to the lower side seam on all polo shirts and to the inside bottom of the placket on all woven shirts
There are to be no buttonholes unopened, missing, too small, stitches broken, incorrect stitch density, poorly formed etc.
All buttons, buttonholes, snaps and components must be aligned All buttons must conform to specifications and must not easily break
Hems
Sleeves and bottoms must be hemmed last, so that the side seams and sleeve underarm seams do not show on the outside of the garment Cover-stitched hems must cover the turn-back raw edge
There are to be no puckered, twisted or uneven hems
There must not be too deep a ‘bite” in the hem that would cause puckering, folding or hem rollover
There is to be no excessive roping or puckering
All hem allowances must be completely caught in the hem stitching
All hem allowances must follow those specified in the Tech Package
There is to be no hem stitching that begins and ends on the front of the garment
Plackets/Collars
All plackets must be interfaced with the correct I compatible interfacing as necessary
Plackets must lay flat and have no bumps” at the base (seam allowances must be closely trimmed)
Front placket must not be crooked from top to bottom
Placket length and width must be as specified
The placket width must be even from top to bottom and must not be distorted
All plackets must be cut and sewn on-grain
There are to be no plackets opening in wrong direction
Top collars must be rolled so that the under collar does not show
Collar points must be aligned and trimmed to eliminate excess bulk
Woven collars must be fused, unless otherwise specified
There are to be no collar points that are improperly shaped, not uniform or that have uneven turnout of edges and points
Neck trim must not be puckered or stretched
Neck opening must not be off-center or skewed
Straps/Belt Loops/Drawstrings/Waistbands
All straps must be reinforced on both ends
Belt loops must be securely attached with bar-tacks on either end There are to be no raw edges on belt loops, unless otherwise specified by design
There are to be no missing, crooked, incorrectly placed, not securely sewn or incorrect number of belt loops.
Belt loops must not extend too far above waistband edge unless specified by design
Drawstring tunnels must have securely attached eyelet openings, unless otherwise specified
Drawstrings must have finished edges
Drawstring ends that do not extend outside of the product must be securely attached with reinforced stitching or bar-tacks on the inside within the casing
There are to be no drawstrings that are not functioning, they must not pull out or expose join seam or internal construction when used
All openings used for drawstring exits must remain secure
Waistband extensions must not be crooked; must be horizontal to the waistband when closed
Closure tabs must not be incorrectly shaped or misaligned
The waistband width must remain even
The waistband curtain must not extend and show over the top of the waistband or the end of a tab
There are to be no waistbands that have excessive fullness, puckering or twisting
All elastic waistbands are to have good stretch and recovery
There are to be no breaking stitches on an elastic waistband when It is stretched
There are to be no waistbands cut on wrong grain
All straps, waistbands, belt loops and drawstrings are to be only those specified in the Tech Package
Labeling/Packaging/Hangtags
There is to be no incorrect label information
All labels are to be positioned as specified
There are to be no off-center labels in the back of neck
All label ink must be permanent
There are to be no handwritten, illegible, incomplete, incorrect or missing care labels, hang tags, packaging labels, etc.
All multiple labels must be properly aligned
There are to be no labels that are cut away with another tacked in its place
All packaging and hangtags must be as specified
There is to be no missing or incorrect packaging
All tags and stickers must have the correct style numbers and other information for that product
Pressing/Specified Drying/Finishing
There are to be no excessively wrinkled products.
There is to be no dampness in any product
There are to be no improperly pressed products
There are to be no press marks resulting from the use of clamps or other holding devices
Any burning, scorching or marks on the surface of product is not allowed
The product is not to be pressed with hard creases where not specified
Mends
There are to be no threads on the inside of the product that interfere with repairs, wear-ability, comfort or appearance
There are to be no poorly done repairs, objectionable mending or noticeable repairs
There are to be no loose strings from repairs on the outside of product
On top stitched seams, a maximum of 4 overlapped stitches will be allowed and the seam must be clipped clean with the thread ends being pulled to inside
Any chain stitch repair must track down in same stitch line as original stitching
The is to be no stopping/starting of any top stitching repair within the focal point of any product (front or near logos)
III. MATERIAL DEFECTS
Materials
There are to be no foreign objects sewn into the product or caught in the seams
There is to be no product or material that does not pass any of the LIQUID GRAPHICS standards when tested by a certified lab
There are to be no discolored or broken yams in fabrics
All fabric and trims must be colorfast
No fabrics are to have a “poor hand”, i.e. stiffness, etc.
There are to be no improper fabric finishes used
Fabrics must not be wrong side out from what was specified
There is to be no excess organic matter or foreign material in product or yarns
No fabric is to be used that does not have good stretch or adequate recovery (especially ribbing or elastic)
There are to be no stubs, runs or misweaves
Thread
Monofilament thread is not to be used, except under special circumstances. These must be discussed with the product developer
All thread, unless otherwise specified. must be dyed to match (DTM)
All thread must be colorfast
Where possible, poly-core thread should be used
There is to be no thread of inferior quality or inappropriate type used n the product
Interfacing
Interfacing must be compatible with the shell fabric in weight and shrinkage
Zippers
Zippers must be of First Quality
Zippers must be fully operative and locking
Zippers must have stops at both ends
All separating zippers must have a right hand pull or as specified in the Tech pack
There are to be no zipper tape colors that do not match the product (if match was intended)
There are to be no defective or malfunctioning parts in any zipper
Snaps/Rivets /Metal Trims
There is to be no nickel in any LIQUID GRAPHICS product
All metal materials used must be non-rusting and non-corroding, with finishes that do not chip All snaps, rivets, eyelets and trims must be securely fastened
Dying/Printing/Embellishing
There is to be no uneven dyeing or printing, unless specified
There is to be no objectionable fade or shade bars
There are to be no objectionable misprints or off-register prints
The tolerance set for crooked logos is no more than 1 in 8
All Logos must be set at the correct angle (See logo angle) All prints or logos must not bleed There are to be no smudges on prints or logos
Washability/Shrinkage
Any product that does not maintain its appearance and shape after five washes and affects the wear-ability or use-ability will be considered a defect
The maximum allowable shrinkage is 3% in width and 5% in length after 5 washings
The maximum allowable torquing is 3% for knits and 0% for woven after 5 washings
The maximum allowable skewing is 3% for knits and 0% For woven after 5 washings
Needles
The correct needle size must be used for all applications
Ball point needles must be used when sewing knits
Needles must only be used in perfect condition and replaced on a regular basis
Holes
There are to be no holes throughout the product, unless intended by design
There are to be no surface holes, blemishes or obvious weaknesses that could develop into a hole
There are to be no snagged or pulled threads or yams
Soilage
There are to be no oil marks, soil marks, spots, ink, etc.
There are to be no rings left after cleaning of soil
There is to be no objectionable odor
IV. FIT DEFECTS
Construction
Corresponding parts must measure the same (e.g. left and rights)
Any key fit measurement must measure within tolerance
There must be no distortion of the balance, drape or function of the product that negatively affects its ability to be worn or used